
Processes
- CNC MILLING
(Vertical & Horizontal)
- CNC Machining
- CNC Turning
- CNC Router
- Prototype CNC
- EDM
We offer expert CNC prototyping services, precision CNC machining services, and plastic CNC prototyping. Our highly skilled workforce operates state-of-the-art machines in our process.

Equipment
- 3 Axis Machining
- 4 Axis Machining
- 5 Axis Machining
(Up to 110" * 72" * 40") - 7 Axis Lathe
- 5 Axis Gun Drill
- Ram EDM
We can mill complex shapes from the toughest materials using our 3, 4, and 5-axis CNC machining capabilities. Our CNC fabrication capabilities ensure speed, precision, and quality. Additionally, our 7-axis lathes and 5-axis gun drilling support intricate geometry and deep-hole drilling.

CNC Materials
- Aluminum Billet
- Aluminum Casting
- Brass/Bronze
- Zinc
- Copper
- Titanium
- Carbon Fiber (SMC)
- Ren Board
- Plastics
- Pine
Choose from our wide range of CNC machining services and materials to get your project done quickly and efficiently. We work with a range of high-quality CNC prototyping materials. These include aluminum, brass, bronze, zinc, copper, titanium, carbon fiber (SMC), ren board, and plastics.
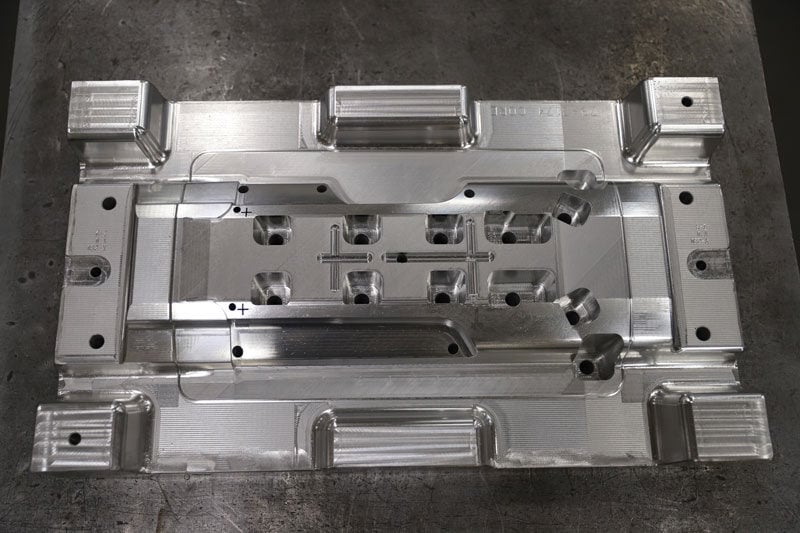
Industries Served
- Automotive (Autonomous)
- Aerospace
- Defense
- Medical
- Consumer Products
- Industrial
Our CNC machining services can be used for a variety of industries and applications. Trust RCO Engineering for all your prototype CNC machining needs.



Why Choose RCO Engineering as Your Go-To CNC Machining Manufacturer?
Our CNC machining capabilities support the manufacturing of various prototypes and production tools. We cater to diverse industries ranging from aerospace and automotive to defense and medical and many more.
Our CNC services offer both high and low-volume capabilities. Low-volume CNC machining enables quick production of CNC prototypes and proof-of-concept parts. CNC machining services for low-volume production have short lead times. This is particularly beneficial for industries with tight schedules.
CNC prototyping services are invaluable for product development. Small batch production allows designers and engineers to test and refine their designs quickly. With all aspects of production under one roof, each department and team can collaborate seamlessly.
When demand surges, our CNC fabrication services can scale production. Businesses can then shift to larger production volumes whenever necessary.
Advanced Technology Meets Diverse CNC Prototyping and CNC Tooling Needs
Our high-speed CNC machining services and precision milling handles all prototypes, production dies, and molds, regardless of complexity.
We use advanced technology, including CNC prototyping machining centers, mills, lathes, and vertical, horizontal, and 5-axis machines. These machines provide fast and precise turnaround for tooling and machine components. Our CNC services include handling gun drills and boring mill equipment.
Wide Range of Materials in Stock
We have extensive CNC machining experience in milling, turning, routing, and EDM. Our fast, reliable CNC services create prototypes and tools from aluminum, brass, carbon fiber, plastics, and more.
RCO Engineering uses cutting-edge machining technology and a wide variety of materials in stock. We have quick turnarounds for soft tooling, precision molds, and dies.
Automated Design
Automated design detects potential problem areas early, reducing reworks and saving considerable time and costs. Enjoy a fast and smooth product development cycle for single or multiple cast components.
Our CNC machining services achieve precise tolerances, providing the prototypes and tooling needed to keep your operations running smoothly.
CNC Rapid Prototyping
We provide CNC rapid prototyping services to help you bring your product from design to market quickly and efficiently.
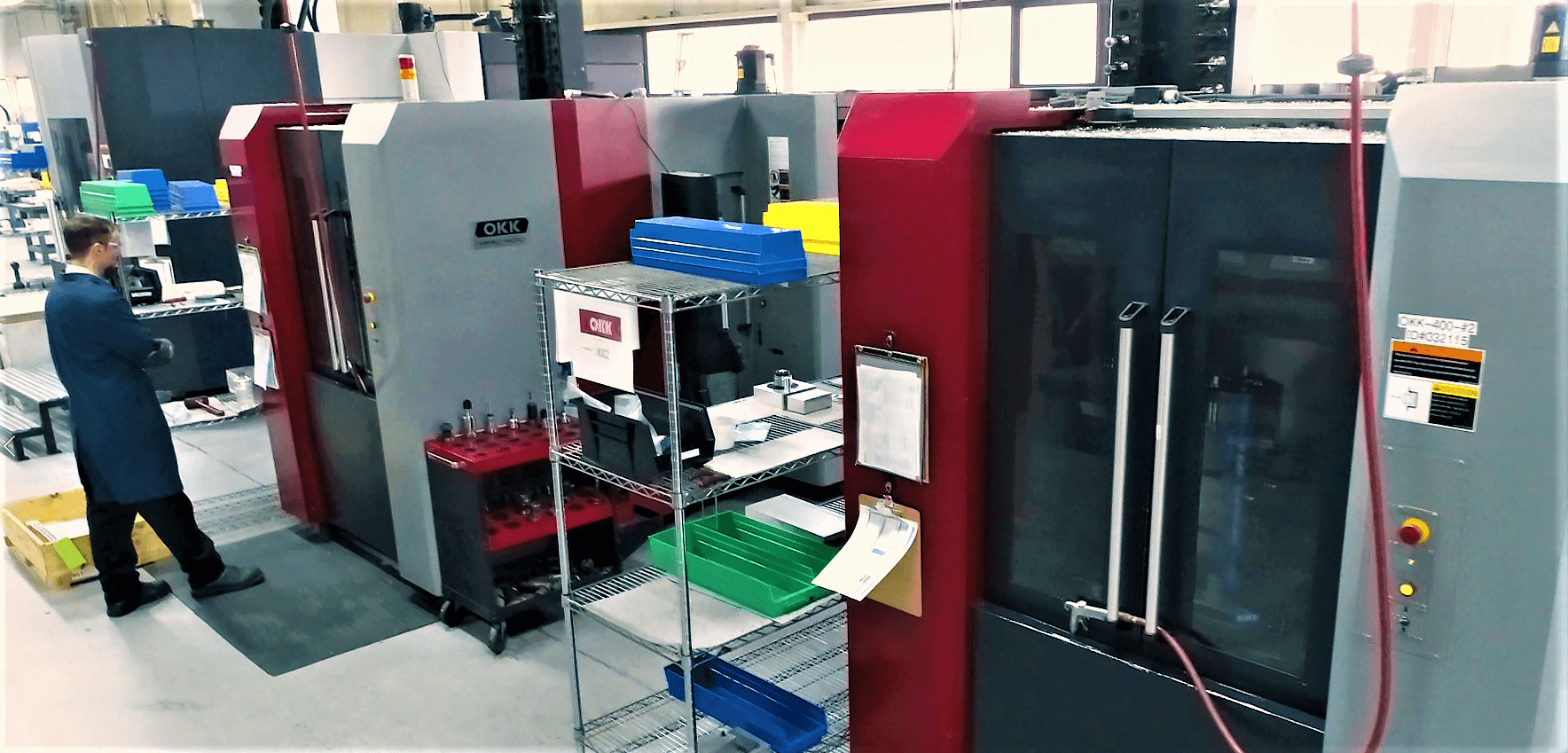
How to Reduce CNC Machining Costs Without Compromising Quality
CNC machining is a go-to manufacturing method for producing precise, high-quality parts across industries like automotive, aerospace, and medical devices. However, the complexity of CNC machining can also make it a costly process if designs and specifications are not optimized for manufacturing efficiency.This guide will walk you through practical strategies to minimize CNC machining costs while ensuring your parts meet performance requirements.
1. Optimize Parts Geometry
Complex geometries require longer machining times and specialized tooling, increasing costs. Simplify your design where possible to streamline manufacturing.
Tips to Optimize Geometry:
Avoid unnecessary tight tolerances: Apply tighter tolerances only to critical features. Standard tolerances (+/- 0.005”) are typically sufficient for most applications.
Design with machinable shapes: Incorporate fillets (rounded corners) instead of sharp internal corners to reduce tool wear and machining time.
Minimize deep cavities: Deep pockets or holes increase machining time and may require custom tools. Aim for a depth-to-width ratio of less than 4:1.
2. Choose Cost-Effective Materials
Material selection plays a significant role in CNC machining costs. Softer materials like aluminum are easier to machine than harder alloys like stainless steel, reducing tool wear and machining time.
Material Tips:
Match material to the application: Avoid over-specifying materials. If strength is not critical, consider less expensive options like plastic or lower-grade metals.
Stock sizes matter: Design parts to use standard material sizes to minimize waste and reduce the need for custom blanks.
3. Consolidate Features
Reducing the number of separate machining operations can lower costs significantly. Combining features into a single setup avoids repositioning the part and saves time.
Examples:
Combine drilled holes into arrays to minimize individual drill cycles.
Integrate multiple operations into a single setup using 5-axis machining if applicable.
4. Reduce Parts Size and Weight
Larger or heavier parts require more material and longer machining cycles. Designing with size and weight reduction in mind can save on both materials and machining time.
Tips:
Hollow out thick sections where possible.
Use lightweight materials if part strength allows.
5. Leverage Standard Features
Custom threads, complex surface finishes, or unusual hole sizes can require specialized tooling and setups, increasing costs. Stick to standard features wherever possible.
Standardization Tips:
Use common thread sizes (e.g., UNC or metric threads).
Stick to standard hole sizes compatible with off-the-shelf fasteners.
6. Optimize Tool Access
Designing for better tool access reduces the complexity of setups and machining paths. Avoid features that require angled or hidden access.
Tool Access Best Practices:
Ensure all features are accessible from a single direction or with minimal tool changes.
Avoid undercuts unless absolutely necessary.
7. Minimize Secondary Operations
Secondary processes like deburring, polishing, or post-machining inspections add time and costs. Design parts to reduce or eliminate the need for these steps.
Strategies:
Use surface finishes that can be achieved directly through machining.
Avoid thin walls that might require additional reinforcement.
8. Order Bulk When Possible
Setup costs for CNC machining are fixed, regardless of order size. Larger production runs allow you to spread these costs across more units, reducing per-part cost.
Pro Tip:
Work with your CNC shop to forecast long-term needs and negotiate bulk pricing.
9. Collaborate with Your CNC Machining Partner
Involving your CNC machining supplier early in the design phase ensures that your parts are optimized for their specific capabilities and tooling.
Questions to Ask Your Supplier:
Can certain features be adjusted to reduce machining time?
Are there alternative materials or finishes that would lower costs?
What are the most cost-effective tolerances for my application?
Final Thoughts
CNC machining is an incredibly versatile manufacturing process, but its costs can quickly escalate without thoughtful design and material choices. By implementing these strategies, you can reduce costs without sacrificing the quality or functionality of your parts.
Working closely with an experienced CNC machining partner ensures you get the best balance of cost, quality, and lead time. Reach out to your trusted supplier today to discuss how to optimize your next project for CNC machining!